Specialist Suggestions on What is Porosity in Welding and Exactly How to Address It
Specialist Suggestions on What is Porosity in Welding and Exactly How to Address It
Blog Article
The Scientific Research Behind Porosity: A Comprehensive Overview for Welders and Fabricators
Understanding the complex systems behind porosity in welding is important for welders and makers aiming for impressive craftsmanship. As metalworkers explore the depths of this sensation, they uncover a globe controlled by various elements that affect the formation of these tiny spaces within welds. From the make-up of the base materials to the intricacies of the welding procedure itself, a wide variety of variables conspire to either intensify or ease the existence of porosity. In this comprehensive guide, we will certainly decipher the scientific research behind porosity, discovering its results on weld high quality and unveiling progressed techniques for its control. Join us on this trip with the microcosm of welding flaws, where precision meets understanding in the quest of remarkable welds.
Recognizing Porosity in Welding
FIRST SENTENCE:
Exam of porosity in welding exposes crucial insights right into the honesty and top quality of the weld joint. Porosity, characterized by the presence of cavities or gaps within the weld steel, is an usual issue in welding processes. These gaps, otherwise appropriately dealt with, can compromise the structural integrity and mechanical properties of the weld, bring about potential failures in the completed item.

To detect and evaluate porosity, non-destructive screening approaches such as ultrasonic screening or X-ray inspection are commonly used. These methods permit the recognition of interior defects without compromising the integrity of the weld. By assessing the dimension, form, and distribution of porosity within a weld, welders can make informed choices to boost their welding processes and accomplish sounder weld joints.
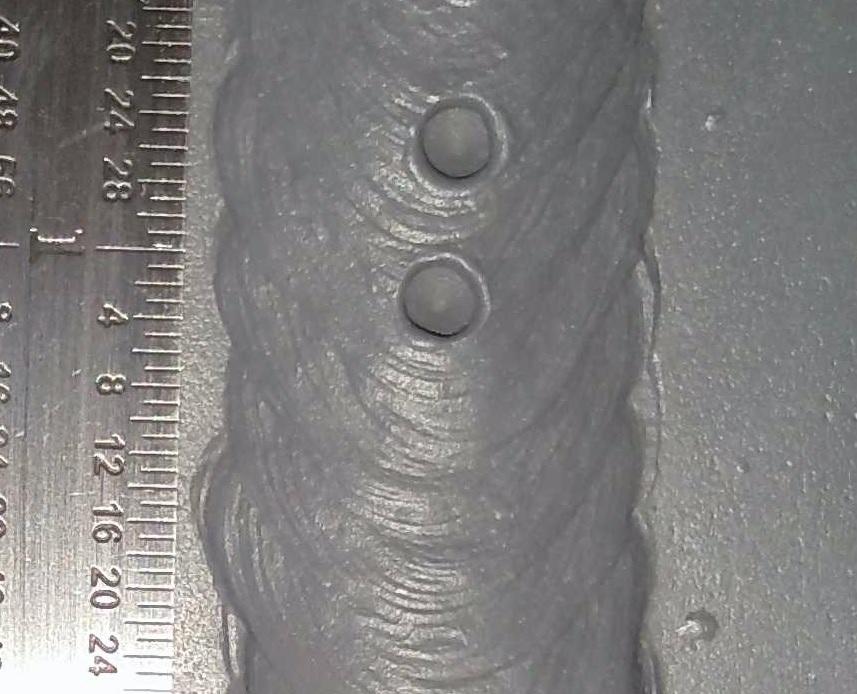
Factors Influencing Porosity Development
The event of porosity in welding is influenced by see it here a myriad of aspects, ranging from gas securing effectiveness to the details of welding parameter setups. Welding criteria, including voltage, current, take a trip speed, and electrode kind, additionally influence porosity development. The welding technique utilized, such as gas metal arc welding (GMAW) or protected metal arc welding (SMAW), can influence porosity development due to variants in heat distribution and gas insurance coverage - What is Porosity.
Effects of Porosity on Weld High Quality
The existence of porosity likewise compromises the weld's resistance to rust, as the entraped air or gases within the voids can respond with the surrounding environment, leading to degradation over time. In addition, porosity can impede the weld's capability to stand up to pressure or impact, more endangering the general high quality and integrity of the bonded structure. In crucial applications such as aerospace, automobile, or structural building and constructions, where security and sturdiness are vital, the damaging effects of porosity on weld quality can have severe consequences, stressing the value of decreasing porosity with correct welding methods and treatments.
Techniques to Reduce Porosity
In addition, using the proper welding specifications, such as the appropriate voltage, present, and travel rate, is important in preventing porosity. Preserving a regular arc length and angle throughout welding also helps minimize the chance of porosity.

Using the appropriate welding strategy, such as back-stepping or utilizing a weaving activity, can additionally assist disperse heat uniformly and lower the chances of porosity formation. By implementing these methods, welders can effectively decrease porosity and generate premium bonded joints.
Advanced Solutions for Porosity Control
Executing innovative technologies and innovative approaches plays a pivotal role in attaining exceptional control over porosity in welding processes. In addition, utilizing advanced welding methods such as pulsed MIG welding or modified Homepage environment welding can likewise help minimize porosity problems.
An additional sophisticated service includes using advanced welding equipment. Making use of equipment with integrated functions like waveform control and sophisticated power sources can boost weld quality and decrease porosity risks. Furthermore, the execution of automated welding systems with precise control over parameters can significantly minimize porosity flaws.
Additionally, integrating innovative tracking and examination technologies such as real-time X-ray imaging or automated ultrasonic testing can aid in spotting porosity early in the welding process, permitting find out here now immediate rehabilitative actions. In general, incorporating these sophisticated solutions can considerably enhance porosity control and enhance the general quality of bonded parts.
Verdict
In verdict, understanding the scientific research behind porosity in welding is important for welders and fabricators to produce high-grade welds - What is Porosity. Advanced solutions for porosity control can even more enhance the welding procedure and guarantee a strong and reliable weld.
Report this page